There are currently three industrial placement students within the Support Labs and one in the Sample Environment teams:
Now that these students have had a chance to settle in and get to grips with their projects, I sat down to interview them about how they were finding the experience.
Gabriel Rosario-Whyte
So, where are you from, what are you studying and where?
I’m from north Essex in a seaside town, but I’m studying chemistry at Warwick, so I’ve been in the midlands and Coventry for the past few years.
What made you decide to do chemistry?
I really enjoyed chemistry at A-level. Well I did the IB [International Baccalaureate], but at that level chemistry was my favourite subject. I also had a really great chemistry teacher at secondary school and that also hugely motivated me to go into the subject at university.
What are you working on now, what’s your project?
So at the moment I’m working as a synthetic chemist. I’m trying to make lipids that we can then use to formulate liposomes, the end goal being to make lipoplexes for gene therapy; so, delivering mRNA to cells in a way that protects the mRNA in the body so it’s not destroyed. At the moment, it’s still early days, but I’ve got a clear plan ahead of me. I’m working on a polymerisation reaction to make the lipids so then I can assemble them and formulate the liposomes.
So, more dangerous question, how’s it actually going?
Step one is synthesising the monomer. Even that’s not trivial but it works. Working as a synthetic chemist, I’ve learned that doing reactions in a lab by yourself, the results almost always aren’t the same to what’s reported in literature. It’s been fascinating learning how much of an impact where in the world chemistry was done plays into the replicability of a reaction. At the moment, the reaction I have been working on has worked – I have a product that matched the literature, but the yield is way off. So at the moment I’m working on optimising the conditions.
So, changing track slightly, how are you settling in?
So, I’ll start with the group: I think I
am getting more settled in. It was a steep learning curve at the start as I’ve never worked in the professional environment of a large company, but I think communication is really key: you
can ask anyone for help. I’ve started to learn that in the lab: don’t suffer in silence! Even if you feel like there is a stupid question, if you just
ask it, then you’re not stupid anymore. So I think I’m getting more settled into the team. ISIS as a whole, it’s really good that there are a few placement students here. I think generally at STFC there’s quite a good student population, lots of things to do outside of work. I’m living in Didcot; that’s really good as well; there’s quite a lot going on for a pretty small town. Obviously you’ve got Oxford too and good transport links to the rest of the country so getting away for a change of scenery once in a while is also really easy.
Do you have any hobbies or interests outside of work?
I do enjoy baking and cooking. I try to do one bake a week and in a way it is similar to chemistry. Especially with cakes, different ingredients can yield different results. Even just baking a sponge cake, and again, adapting a recipe to what ingredients you have in your kitchen or to get the kind of sponge you like is just the same as optimising reaction conditions. At the moment the recipe I’m following for an Old-Skool sponge cake says to use four eggs. Four eggs seems a lot to me and the more eggs you add to a cake, the denser the cake sponge will be. So as a chemist I find that interesting!
Plus for this one you get to eat the results.
Yeah, which is a bonus too!
Hannah Alexander
Could you want to briefly introduce yourself please?
I’m Hannah Alexander, I’m from North Devon and I study at Sussex University.
What subject are you studying?
I’m doing an integrated Masters in chemistry.
So, what made you decide to study chemistry?
I’ve always been a huge fan of science; at college I did a BTEC in Applied Science and found the applications of chemistry the most interesting. For me it has the perfect balance of theoretical and practical techniques. Plus, the fact that Sherlock Holmes has a Master's in chemistry inspired me to do the same, I've always been a huge fan!
What are you currently working on, what
is your project?
My main project at ISIS is Ferromagnetic resonance and we’re developing a high-power version of the setup to improve the results for analysing magnetic thin films. It will also be used on the POLREF beamline.
Slightly dangerous question, but how’s the project going?
It’s going well! I'm proud of the progress I have made since starting here at ISIS. There was a period of getting into the swing of things initially – as with anything - but it all feels very progressive now. I have done a lot of background reading and preparation for my next steps, and I recently overcame an issue we were having with the microwave amplifier. It feels great to have all the preparation work pay off!
So how would you say you’re settling in here in the team, and at ISIS in general?
Yeah, I really like it, I think it’s a lovely place to work. I feel I know everyone in the group quite personally and everyone’s really chatty and friendly, and then ISIS as a broader group is also great: I love interacting with people from other teams, like electronics, cryogenic and the soft matter team, all the people that I just see day to day I like having a chat with. I really like the social aspect of it.
Outside of work do you have any hobbies or interests?
Yeah, I’m quite an active person, I love all sports and activities. I like living in Didcot because it means I can cycle to work (when the weather allows for it!). I love swimming in the rivers nearby; just anything outdoors in nature really!
Anything else you’d like to add?
I’d just wanted to say, having the opportunity here to do my placement has been really great and I think it will benefit my future, degree and career massively.
Luke Broughan
Tell us a bit about yourself; where are you from, hometown, education etc.
My name is Luke, I’m Irish (I’m from Dublin), I’ve been going to Uni in Warwick for the last 3 years, and I’m a Masters student here at ISIS.
What subject are you studying?
I study Biomedical sciences.
So what made you decide on Biomedical science?
Well, I was always going to be a scientist of some description, it was the only thing I ever seriously considered. I bounced between being interested in different branches of science, but I had a
really great biology teacher in sixth form and it just made me kind of fall in love with it: the complexity and the ability for it to make a very tangible difference to kind of everyday life for people; the development of medicines and biologically-derived technologies was just very interesting to me.
What’s your current project?
So, in order for biological molecules to be compatible with neutron techniques they need to be deuterated. My project is effectively to develop a way to grow bacteria in such a way that they become deuterated and then squeeze different bits out of them, different biological molecules. At the moment, we’re interested in LPS which is the outermost layer of lots of bacteria, but really it’s quite a broad project that is effectively just developing a method for efficiently, cost-effectively producing deuterated bacterial molecules, by deuterating the bacteria themselves.
Okay, so now the dangerous question: How’s it going?
It’s going pretty well, I think. I mean, I’m very self-critical so if I’m being honest, I never feel like I’m doing as much as I could, but everything seems to be on track. I think I’m putting a little bit of an unexpected ‘spin’ on the project because the original brief was
just producing these deuterated biological molecules, just kind of going all the way through to that, but for me, from a more ‘pure biology’ point of view than lots of other people here I’ve developed an interest in the bacteria themselves, rather than proceeding all the way through to just squeezing the stuff out of them, you know, characterising them biochemically and characterising the cells themselves on the neutron beamline, so we’re setting up to do that next weekend; we’re running bacteria on the SANS2D instrument. We’re going to do biochemical characterisation of the cells and effectively see what life in deuterium does to bacteria and then we’re obviously going to proceed to extracting membranes and LPS’s from them; we’ve done a pilot for that actually, yesterday, in fact we’re still doing it! It’s going well! I think I’m putting an unexpected spin on the project that just comes from my perspective as a pure biologist.
Changing track slightly, how are you settling in here?
As soon as I visited here for the first time, I got the same impression as when I went to Warwick for the first time, which was that everyone is
really nice, which is always a good sign in a place! Everyone is really supportive of you, and everyone is endlessly giving with their time and expertise, which is very useful, especially to me as someone who is a little bit of an outsider, a) as a student and b) as a biology student, very much a minority. It’s really nice that everyone is so giving of their time, and willing to train you in things that aren’t your area at all.
So would you say that’s the team or ISIS as a whole?
The group is great, but it extends even beyond the group to, like, instrument scientists at ISIS, and we have a partnership now with the Research Complex because we have to use some of their facilities, so we’re in touch with them. We have the support of the other neutron sources; I love that there’s this eclectic global community of people that are all interested in this incredibly niche but powerful technology. I like that a lot.
Outside of work, do you have any hobbies or interests?
I think my biggest interest is probably music. I’m pretty musically-untalented, but I’m very interested in how music is made and recorded, and how audio is engineered. I’m really into the progressive rock bands of the UK and US of the 70s and 80s, that’s my main genre. I’m really into going to concerts and stuff like that, so that’s definitely my biggest interest, so I’m never far from my headphones! I’m quite interested in astronomy, and I love that here I’m very welcome to see the astronomical research that goes on, and help out with the Stargazing event for example; you’re very welcome to branch out into that.
Lucy Bain
Let’s start with a bit about you: What’s your name, where are you from, what are you studying?
I’m Lucy, I’m from Lancaster and I’m studying Natural Sciences at Loughborough University. I’m doing a placement here at ISIS in the Cryogenics team.
What’s your current project?
Currently, I’m working on Ultra Low Temperature (ULT) noise thermometry, using a SQUID magnetometer. Hopefully we’ll be using that to calibrate lots of ISIS ULT devices. It’s pretty simple to use, so I am hoping it can be used in a lot of future projects, like analysing beamline heating on samples at ISIS. Alongside that, I’m helping the cryogenics team with the run and cooling cryostats, prepping dilution fridges etc.
Slightly dangerous question: How’s the project actually going?
I think it’s going okay. Definitely a few hiccups in the beginning: I broke a cable and had to re-solder it or the fridge didn’t get to base. But yeah, I have it working now and I believe it will be helpful for the cryogenics team in the future; being able to reliably calibrate precise temperatures, so I think it’s going well.
How well are you settling in to the cryogenics team?
I think now I feel very settled in where I am. The team is *so* friendly. Everyone’s really down to earth and easy to chat to. They are all so nice: just ask for help, everyone’s happy to do so. And with Lancaster, the university is known for low temperature physics, so in the beginning it was quite nice for me being from Lancaster to relate with my manager who’s been there, so just a really nice stepping stone to settle in.
Do you have any hobbies or interests outside of work?
Yeah, I’m really into sport, specifically football. I really love to watch and play football, even though I mean, I support Manchester United so it’s not a great time at the moment, but I do enjoy that! I also like to cook, to cook for people, going outdoors, just simple stuff like that.
Any other comments? (‘No’ is a fine answer if not!)
I just appreciate the opportunity to work in ISIS. The whole environment is so lovely, everyone in all departments, so I really appreciate the opportunity to work at such a great facility!
STFC ISIS has had a strong apprentice programme for (many years), which has been vital for the continued smooth operation of the Sample Environment teams. This is a major route through which keen new talents are inducted into the various Sample Environment teams, allowing for succession planning for staff nearing retirement, and ensuring that knowledge can be transferred intergenerationally. Since it's not possible to hire apprentices without open positions to fill, it's important that those positions are available.
At the same time, the apprentices gain valuable hands-on experience across a wide variety of work areas, rotating between teams on a (how long? consistent across teams?) basis which will serve them well, regardless of whether or not they continue on with ISIS. Some examples of the experiences the current apprentices are able to experience are given below, and have been mentioned in previous issues of the SEaSL newsletter as well.
For more information about the apprentice sceme at ISIS please contact (Oleg?).
Hello, my name’s Thomas and I am a part of the STFC apprenticeship program. I’m a second year mechanical engineering rotational apprentice. In this apprenticeship I spend 4 months in different placements, in different departments around RAL site. I am nearing the end of my second placement which I have spent working with the Pressure and Furnace team. During this time, I’ve learnt what they do and why. I've also learned a variety of skills like welding, pressure testing and leak detecting.
One technique that I learned whilst working with the Pressure and Furnace team is spot welding. Spot welding is an operation in which you apply pressure and send an electric current through two metals. The internal resistance in these metals causes them to heat up and join. The Pressure and Furnace team use spot welding to create sample cans (For the ISIS user’s samples), heat shields, furnace elements and thermocouples.
Another technique that I have learned in the Pressure and Furnace Lab is orbital welding. Orbital welding is similar to spot welding however, rather than welding a small precise area at a time, it is used to weld around a diameter. This process is used to connect pipes and fittings by rotating an electrode around the join between the two pipes whilst sending a current through to heat them up and weld them together. The pipe gets so hot that we need to flow argon gas through the pipes to keep them cool. We use argon gas because it is an inert gas, meaning it can displace the oxygen around the join, preventing oxidisation whilst welding while not reacting itself. Whilst creating a piece with the orbital welder, I needed to use the micro-head welder to get to parts that the normal weld head could not. The micro-head welder works the same way except it has a smaller clamp. This is helpful for welding in hard-to-reach areas although the smaller clamp also means that there is less stability, increasing the chances of failure when using it. Having multiple problems with the micro-head welder, I decided to base my apprenticeship project on creating a clamp to make it easier to use.
One of the most important operations used by the Pressure and Furnace team would be leak testing. Leak testing is a process in which you spray helium onto any joints and pipes in a gas system under vacuum and then use a helium detector to sense any helium that enters the system. We use helium because it is an inert gas meaning it does not readily undergo chemical reactions and therefor ensuring that it is safe. Another reason we use helium is because it has very small molecules meaning it can find smaller leaks. This process is necessary for multiple reasons. One of these is that the panels created by the pressure and furnace team are usually used by the ISIS users. This means that lots of different gases can be flown through them including flammable and explosive ones. If there was a leak in the system that had not been detected, these would leak out and could cause a serious hazard. Below, is an example of the system used when leak testing.
Proof testing is very important in the pressure and furnace section. It is used to test anything that will hold pressure in its normal use. This includes things like cells and pipes. To do this, you first attach the object being tested to the pipe in the bunker. You should then step outside the bunker and close the door. The door is very thick and made of metal to protect the operator and others from projectiles if the object being tested were to fail. We then fill the vessel up to the testing pressure. We calculate this by multiplying the design pressure by 1.25. The design pressure is the pressure that the vessel was designed to be able to hold so it is safer at its working pressure. This is calculated by multiplying the working pressure by 1.1. This means that if a cell needs to work normally at 1bar, it should be designed to work at 1.1bar however should be tested it at 1.4 bar. Next, we leave it for 30 minutes and then check back to make sure it hasn’t leaked. If it doesn’t leak, it then needs to be engraved with an RLI number. Throughout the proof testing process, there needs to be an authorised proof testing witness. This is to ensure that all tests are done properly.
Theo Guibarra
I have enjoyed my time in Soft Matter and feel it has been a fantastic experience for me. From day one, the team was great and treated me with respect, kindness and equality, and they were always keen to include me, help me and show me new things for which I am grateful. This type of technician work, as well as the environment in ISIS TS2, is very different to what I was previously used to in the workshop, so it has been very eye-opening. I have developed skills such as CAD, design/development, communication, and assembly. I have also gained my 2-tonne crane license, experienced chemistry work in the Deuteration lab, and got exposure to working with new equipment such as magnets, cooling/heating systems, compressors, pumps, cryogenics, pressure vessels, and other equipment used on the beamlines to facilitate experiments. I have also had the pleasure of working with some of the beamline scientists and users.
The finished mounting plate with its drawing.
One example of this was at the beginning of the placement when I was tasked with aiding one of the beamline scientists. Rather than being told exactly what to do or being given an easy apprentice job, I was treated like any other technician and liaised directly with the scientist.
Left: Using a scissor jack to determine the required height; right:
The final assembly of the stand supporting the Linkam box.
First, I set up a meeting with him to discuss what he needed and used this as an opportunity to take measurements and pictures of the equipment. The task was to design a stand sturdy enough to support the Linkam box containing the sample, suspended in the centre of a large set of magnet coils. Because it would be used in a magnetic field, I decided to use aluminium so it would cause minimal interference with the experiment and reduce the risk of damage to other equipment. To ensure its compatibility with the existing height stage and the Linkam box itself, I decided to design two adapter plates which would mount onto each of these respectively. I then designed a support column to gain the remaining height necessary while maintaining stability. The drawings were then given to the R6 workshop to be machined before assembly and final installation on the Zoom beamline.
Verifying the temperature using a handheld digital thermometer.
Another job I was tasked with early on was testing a four-position heater stage. After receiving reports that the heat stage had been displaying incorrect temperature readings and inconsistently holding temperatures, I was asked to conduct some tests to verify the accuracy of the heat stages and the PT100 temperature sensors. After all the tests were complete, I wrote a report detailing my test methods and conclusions, as well as a guide on how to safely set up and operate the heater. The final part of the job was to clean and regrease the heaters and the sliding mechanisms to ensure they were functioning properly and efficiently.
Elliot Slade
During my time in Soft Matter I was given many opportunities to work on various projects, such as designing a sample plate to be used on SANS2D. I was able to develop my CAD, assembly and communcation skills. I met and worked with the beamline scientists and users and learnt about their experiments and wasable to help setting some up.
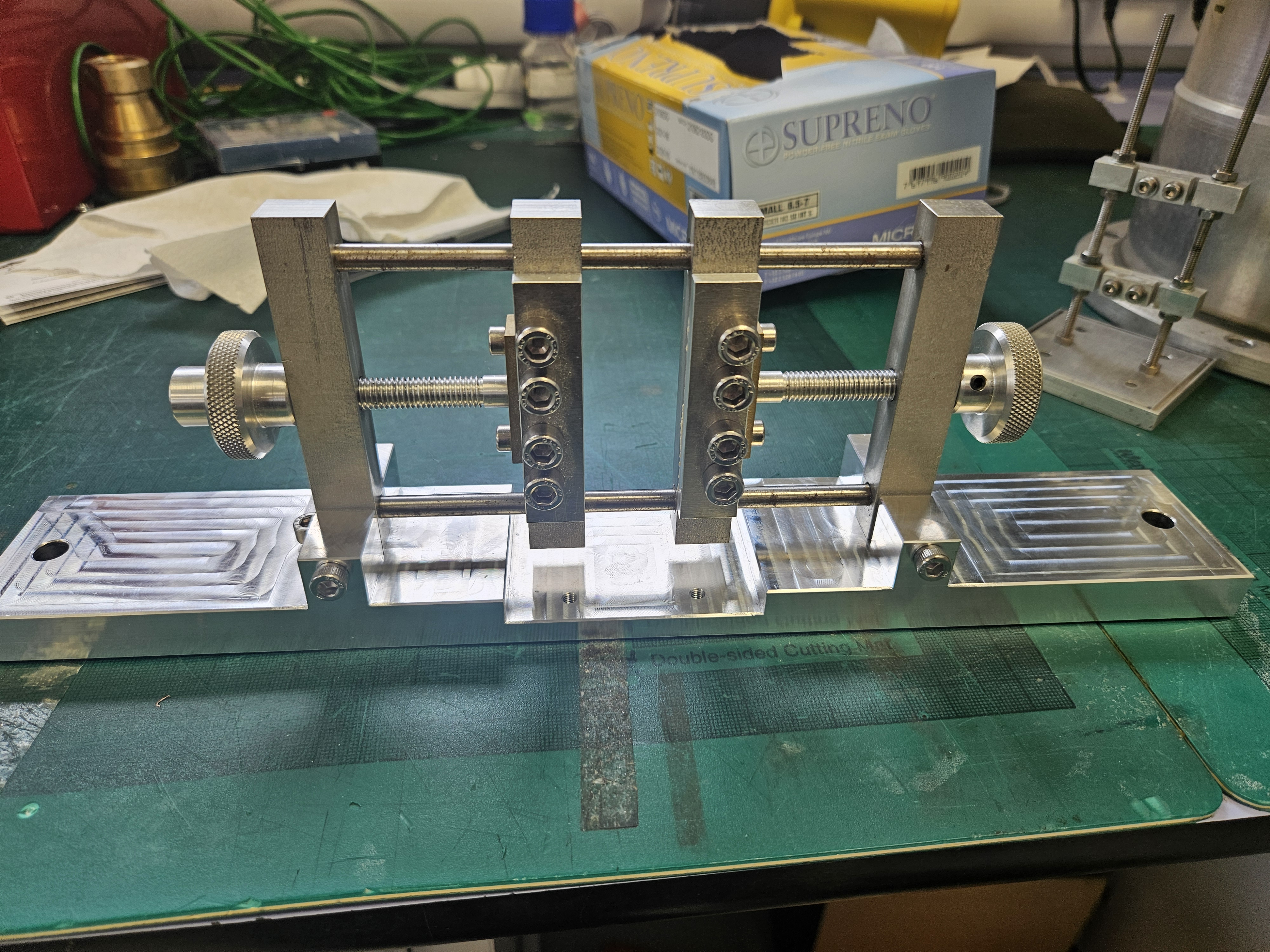
The sample plate is designed to hold both vertical and horizontal stretchers for the instruments.
I was also given the opportunity to spend some time in the deuteration lab and do some chemistry which I enjoyed, and I spent some time in the FLYNN Lab learning about polarisation. Overall my time in Soft Matter was very enjoyable and a good learning experience.