After being approached by a local GP who was finding it difficult to get hold of the additional visors needed to protect their staff during the coronavirus pandemic, Erik Johnson from the ISIS Instrument Support team wanted to find a way for his team of mechanical technicians to be able to help. “I was looking for something we could all do whilst still working from home. Any 3D printing work would have required going to back to the lab, but I wanted our staff to remain in their houses."
Technician Josef Lewis was tasked with researching different concepts and designs to see if there was a method they could use to produce face shields at home, using materials they would be able to buy off the shelf, rather than make themselves. He found an open source design for a 'Badger Shield' and contacted a range of companies who sent out some initial supplies. This enabled him to make a prototype and develop it into something that the rest of the team would be able to make quickly and easily. “From concept, through prototype, to manufacture, took only four days!" he explains.
After delivering the first few visors on 4 April, Josef ordered in enough materials to ramp up production: he now has enough to make over two thousand! Once the materials have been delivered to Josef, he sorts them into bundles for distribution amongst the 15-strong team of technicians; “my utility room has become a goods out station!"
To accompany the bundles, he has also produced a short tutorial video explaining how to assemble the visors. All the volunteers need to ensure that the space they use to make the visors is clean and tidy, and they are careful to wear gloves and masks during assembly, and immediately seal the visors in zip-lock bags for delivery.
Although the face masks do not have CE markings, and are not medical grade, they provide an extra layer of protection that these front line workers are finding very valuable. In the last week the group have had contact from sixteen organisations in the local area, who have found them purely by word of mouth. These have been GP surgeries and pharmacies, but have also included the Churchill Hospital Renal Department, Northampton Hospital Radiography Department, and other research institutions on the Harwell Campus.
Despite being such a small team, over 400 visors have already been distributed, and are being very gratefully received; “the clinicians here at Broadshires are all in agreement that the face shields are excellent, they are robust but also comfortable to wear for sustained periods without having to remove them, and also give them much needed confidence and protection when seeing patients face to face;" Trevor Warner, Practice Manager, Broadshires Health Centre.
On a normal day at ISIS, the Instrument Support team would be upgrading beamlines and detector systems. However, with the need to work from home, the team are glad they are able to use their time on such a valuable project. Erik explains; “it's brilliant. The whole project demonstrates the expertise and skills of the technicians at ISIS. Their inventiveness, and the ability to work so quickly has really been showcased here."
“Our ability to react in the moment, and deliver an end product, is something we need to do regularly in our roles, and that has really helped," explains Josef; “It means a great deal to me to be able to support our country in this way and it makes me very proud."
In addition to those working on visor production, other members of their team are busy training ventilator testers, as part of the Ventilator Challenge UK consortium.
ISIS Director, Robert McGreevy, added; "These tasks are somewhat simpler than the challenges of normal ISIS operations, but those obviously can't be undertaken from home so it is great to see the group turn their hand to supporting the national effort."
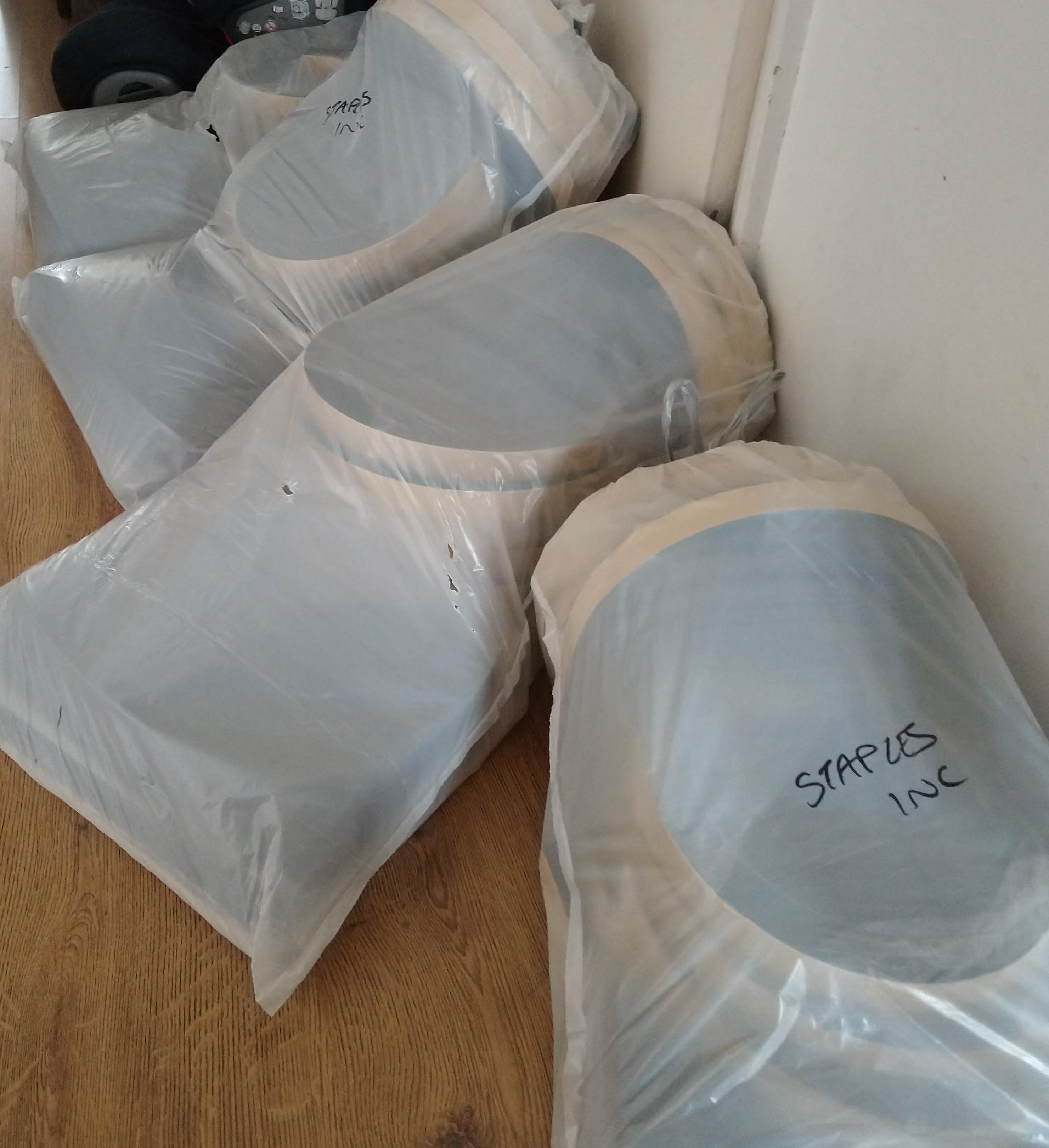
The visor materials bundled for distribution. to the other volunteers.