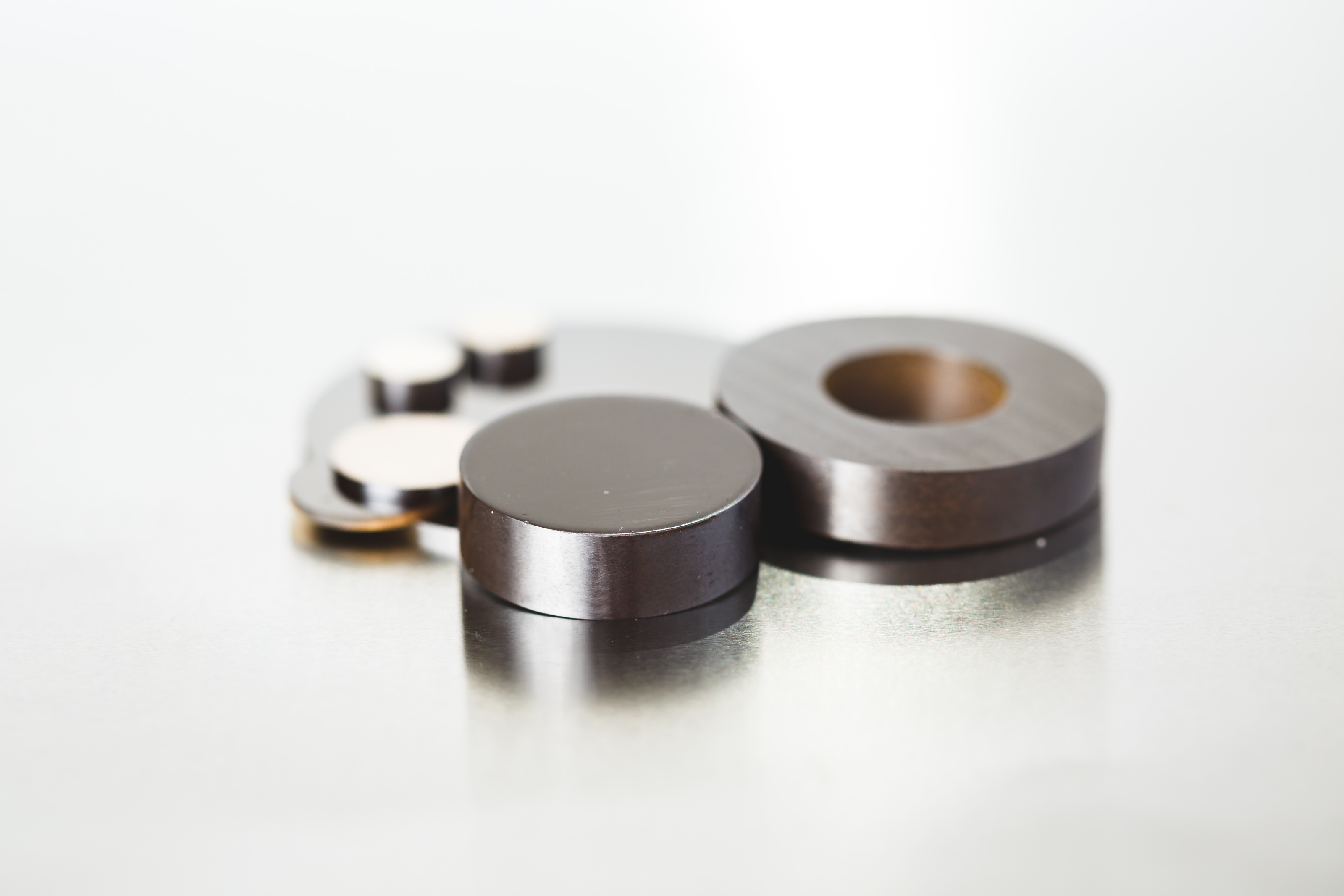
Piezoelectric materials share the unique ability to generate electrical charge from mechanical stress. If you squash it, you can make electricity; vice versa, if you apply electricity they generate mechanical strain. A wide range of naturally occurring materials have this property, but for industrial applications synthetic materials are used, with their properties tuned to meet the application. The range of applications are broad, from cigarette lighters to loudspeakers, inkjet printers to ultrasounds, piezoelectrics permeate our daily lives and represent a growing annual $15bn market.
“Piezoelectric materials are ubiquitous in industrial and commercial sensing and actuation, but until recently they were limited to relatively low temperature environments. We set out to understand what the limiting factors were at the atomic scale, by studying new and existing materials with novel in-situ crystallography experiments and using this understanding to design materials that can operate reliably in challenging environments”, says Tim Stevenson (below), Development Director at Ionix Advanced Technologies, a spin-out from the University of Leeds.
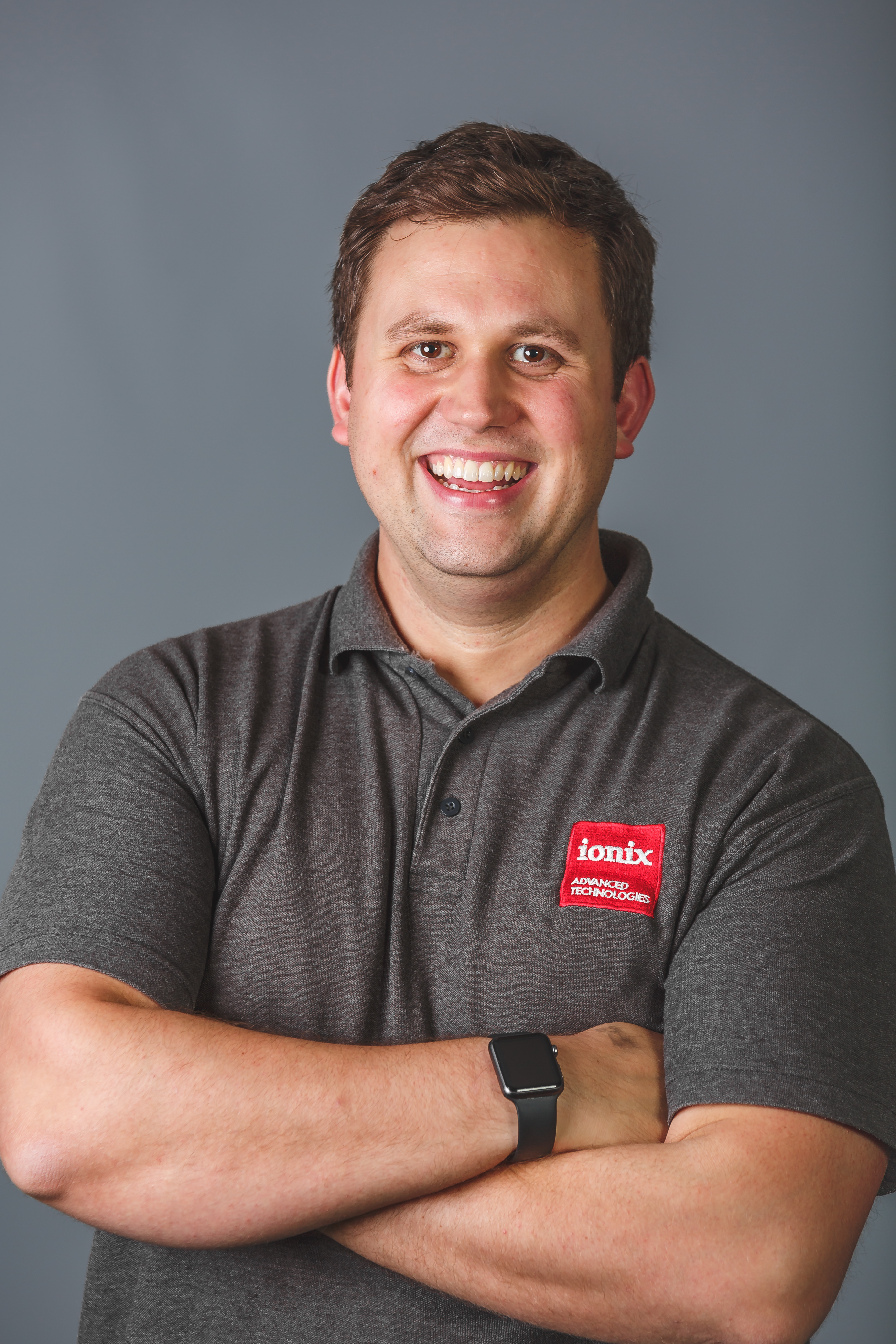
Tim Comyn, Technical Director at Ionix, adds, " The increased contrast, resolution and speed of data capture gained from using neutrons and high intensity X-rays respectively was vital in the development of our product. Crystallography as a function of applied electric, magnetic and mechanical fields provided the insights we needed to understand why existing materials failed and how we can refine their properties, so they can perform in more demanding environments."
The group used several instruments at ISIS and
Diamond Light Source to help develop a range of new materials that can perform in these challenging environments without compromising on performance. As of 2018 Ionix employs 17 full-time staff and offers a range of products based on their unique piezo-ceramics to the oil and gas energy, nuclear and aerospace sectors.