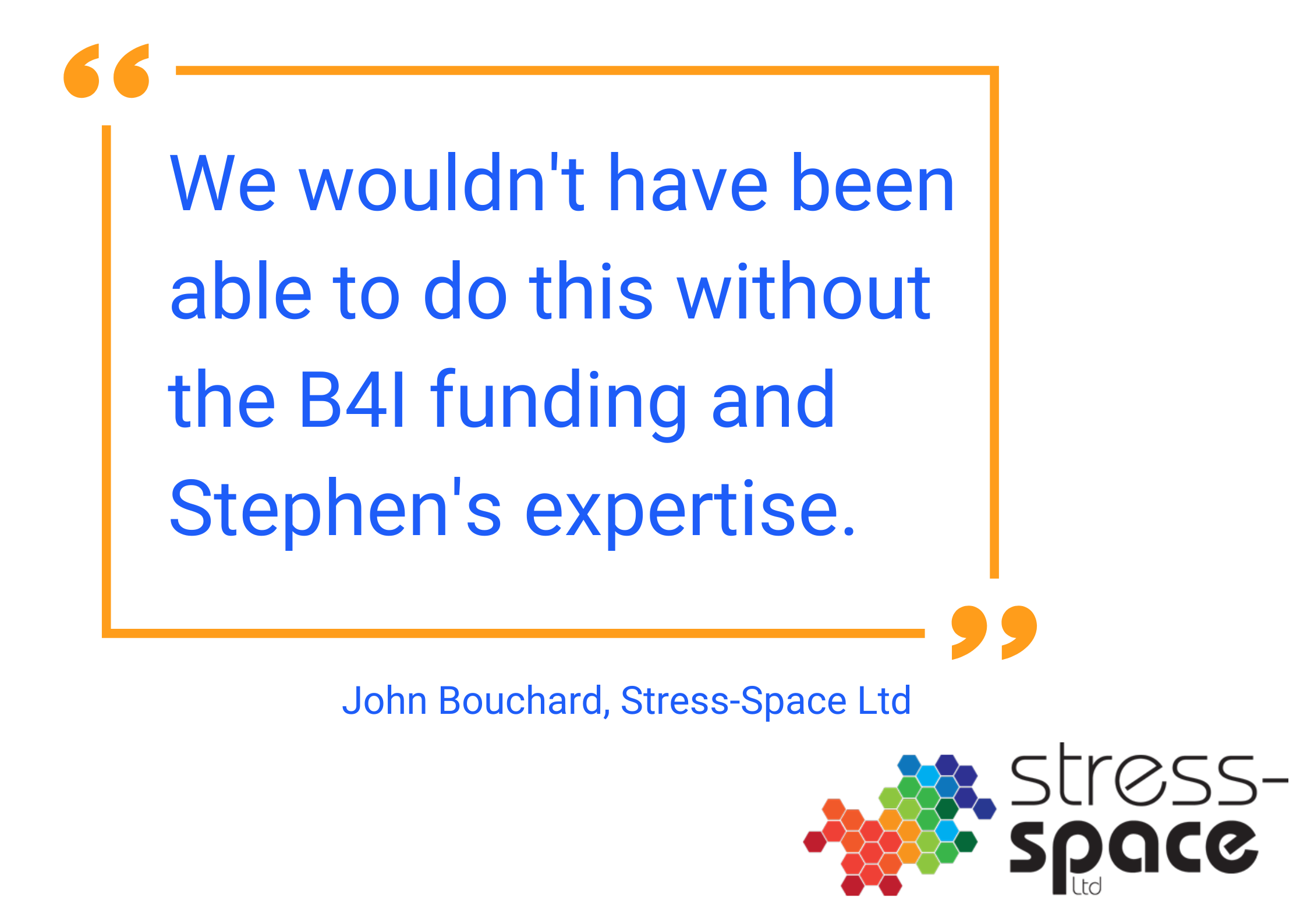
Stress-Space Ltd (SSL) was founded in 2017 by research staff from the Open University, offering residual stress measurements to clients in the space, energy and transport industries. They help validate the design, manufacture, inspection and performance of engineering components. With the support of Stephen Nneji from the Research Software Engineering group at ISIS, they have developed an adaptive robotic X-ray diffraction system to enable them to map surface residual stress across complex structures.
Positioning the objects so that the X-rays are focused on the correct point is challenging, especially for complex “real world" shapes. SSL Founders Dr Sanjooram Paddea and Professor John Bouchard had an idea that could solve this issue; “If we could scan the surface geometry, then we could use this scan to guide and position the robotics precisely. We were aware that Stephen had written software for controlling similar instruments at ISIS, and so we approached him to help us develop a system of our own."
After initial funding from the ESA BIC UK Incubation Programme, the software was progressing, but it wasn't as easy as expected. Thanks to additional funding from the B4I programme, Stephen was able to continue working with Stress-Space to solve their issues.
“We were trying to solve the hand-eye calibration problem," explains Stephen. “The X-ray system and scanner are both mounted onto a robot, where the scanner is eye and robot is the hand. It is crucial to know exactly where both of these are in relation to each other and the object. However, because the optics are all inside a metal box, you cannot measure this directly. Instead, we designed a laser scanner that can be attached to the robot, and developed coding that makes the system accurate, as well as being fast and easily operated."
His solution proved to be robust and benefitted the small company. “We are intensively using it and it is a pleasure to use," says John. “The original system was very labour intensive and non-intuitive. This has sped up our setup process by a factor of ten, which means we can use our time better elsewhere. It also means we can now run the experiment remotely, including being able to map out large surfaces overnight and monitor it remotely."
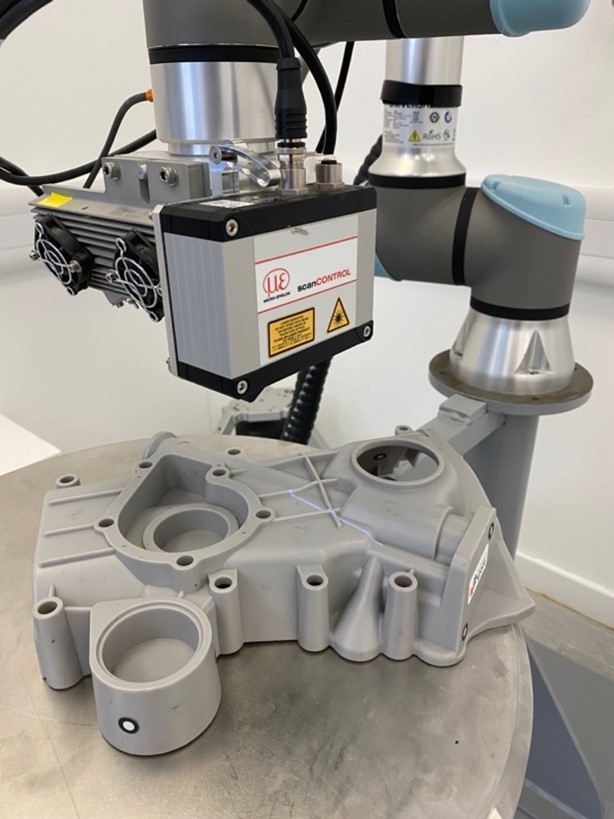

Adaptive system laser scan of surface (left) generates 3D model (right) that is used to define locations and directions of interest.
With the new adaptive system significantly enhancing capability of the original diffractometer, SSL have supplied it to the manufacturer MRX-rays who, after testing, have begun to sell it fitted to their new instruments. The adaptive robotic technology will also be of interest and value to wider industrial applications in the future, for example non-destructive ultrasonic inspection of equipment installed in aggressive environments.
As well as benefiting the company, the experience of collaboration enabled by the B4I programme has also been valuable for Stephen; “being able to work on the robotic and scanning system was new for me. Although you learn about the theories, it's not often you get to apply them, so it was a great experience for me to work with a company that was applying the software in real life."