The Soft Matter Team have chosen to highlight the work
conducted to intergrate the ISISstat and Delft Furnace into the user programme.
Contents:
General Updates
ISISstat
In their latest project in Soft Matter, the team successfully revived the previously underused 'ISISstat' cryostat, originally owned by the Cryogenics department. The Soft Matter section adopted this equipment to enhance their beamline experiments. After rigorous testing, including checks on the compressor, mercury rack, cryostat, and cold trap, the team confirmed the system's efficiency in reaching and maintaining a base temperature of 3 Kelvin.
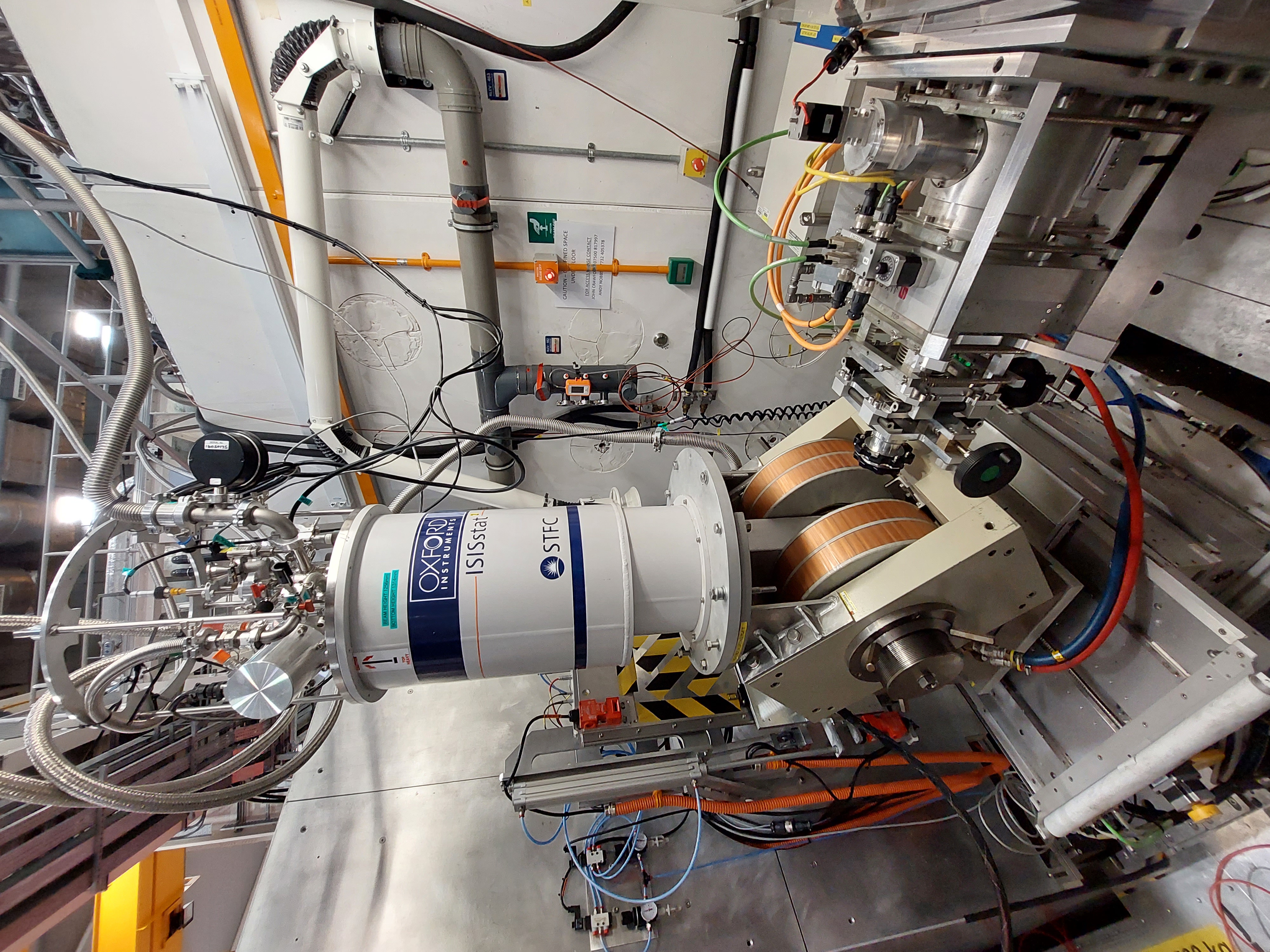
The venerable ISISstat.
The introduction of nitrogen autofill’s has significantly improved the system's operation, enabling it to maintain the base temperature continuously for up to a week without the need to manually refill the cold trap. This upgrade has boosted the experimental capabilities, as demonstrated during its deployment on the ZOOM beamline, where it achieved and sustained the required base temperature throughout the experiment.
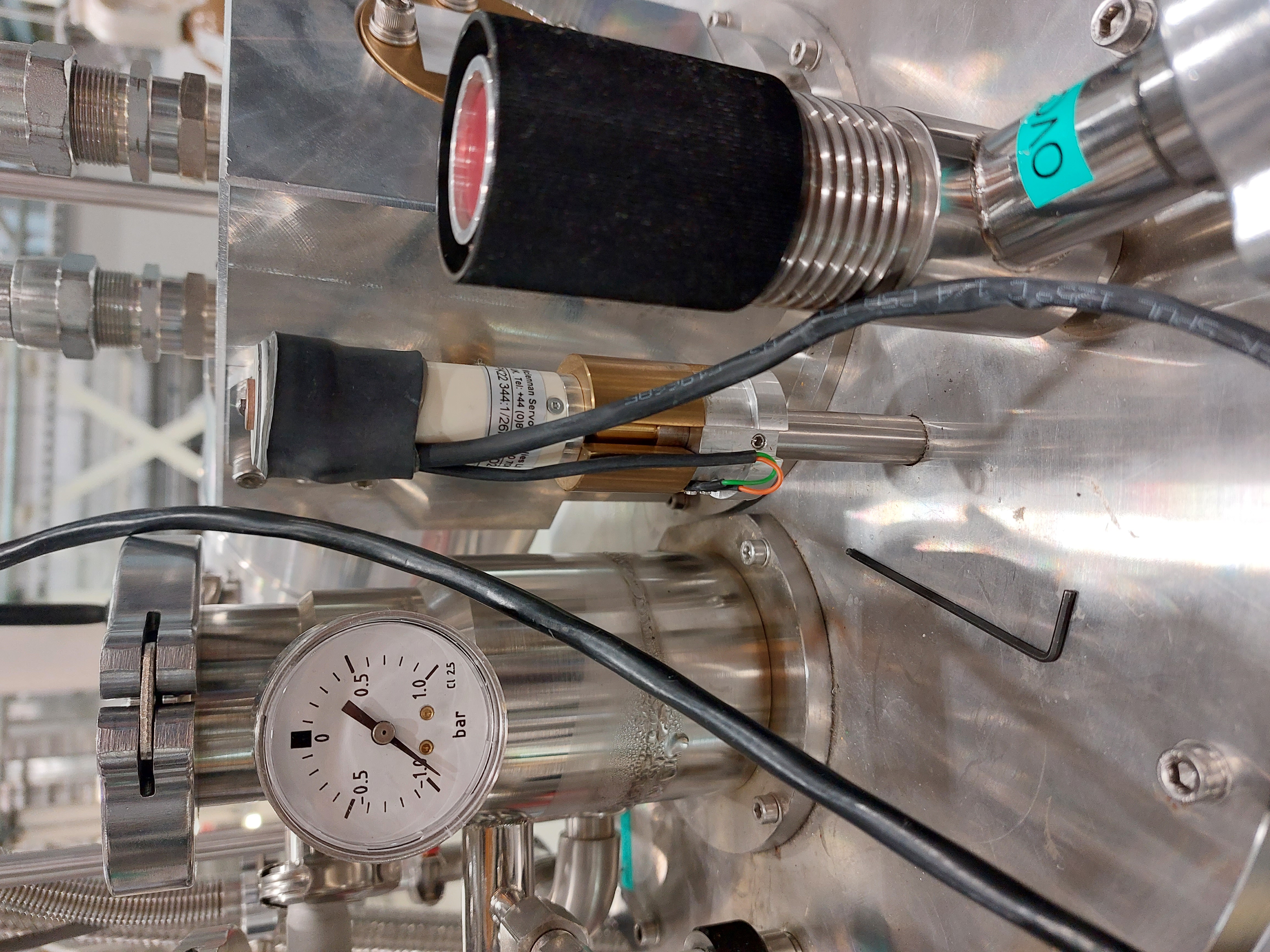
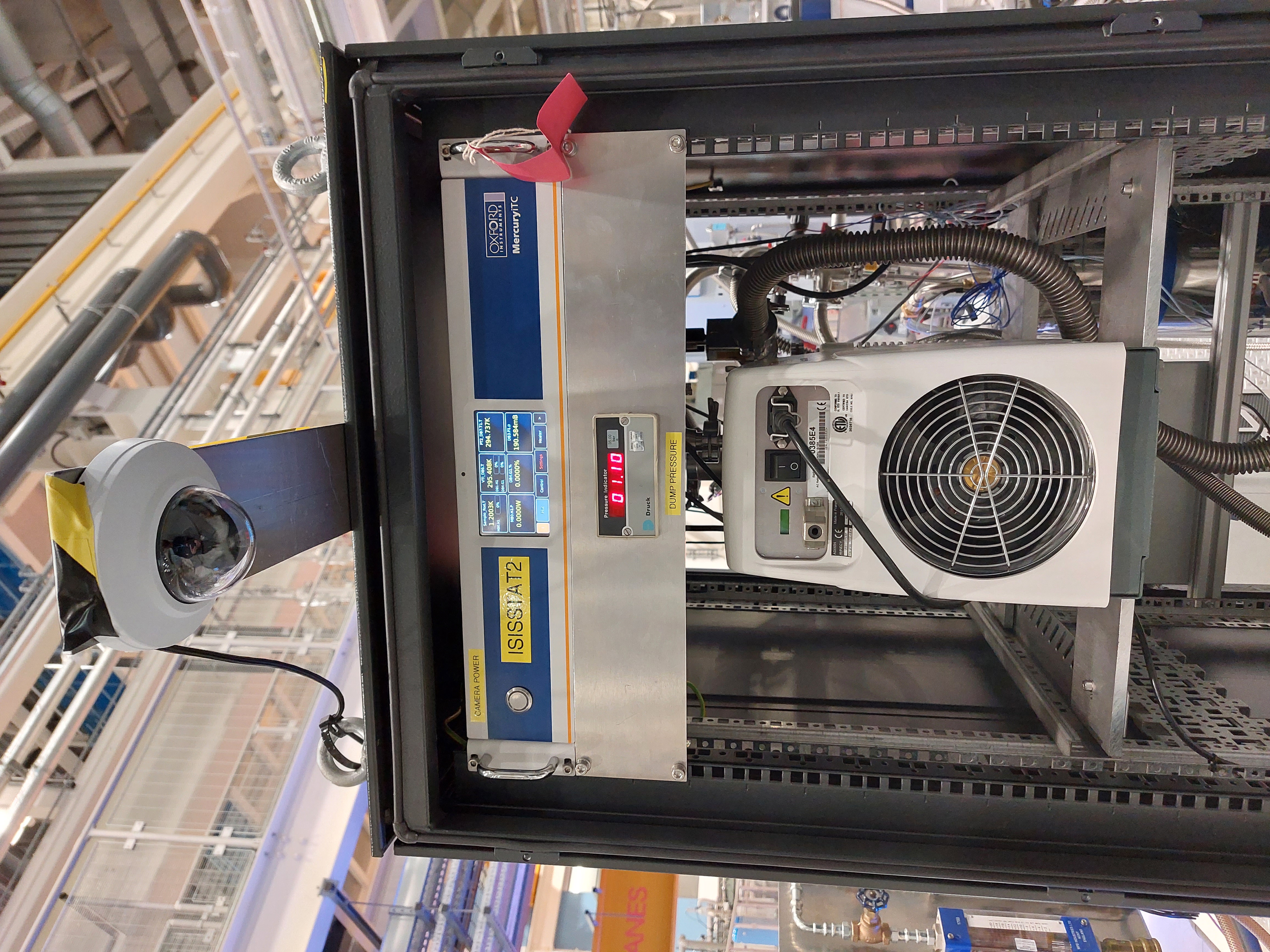
Left: Automatic needle valve, Right: The installed remote-operation camera.
Further enhancements included installing a camera on the mercury rack for remote monitoring and an automatic needle valve for adjusting the flow rate remotely via IBEX. These upgrades have not only simplified the monitoring and handling of the system but have also expanded the experimental tools available. The team now has a cryostat that can be integrated within a GMW electromagnet on the beamline. This project has successfully reinstated a key piece of equipment and enhanced the team's technical skills and capabilities.
Delft Furnace
The Delft furnace is a compact quenching furnace on loan to ISIS from the Delft University in the Netherlands. The design means it can sit between our GMW magnet poles, allowing a magnetic field to be applied to a sample whilst heating it or rapidly cooling it. The Furnace can be pumped out to create a vacuum or an inert gas can be flowed in the sample chamber.
A LARMOR experiment in December 2023 investigated Oxide-dispersed-strengthened steels and welds and their precipitate evolution and optimum tempering temperature. The furnace was therefore ideal as it allowed for heat treatments to be applied to the sample.
Harry Oliver designed a sample holder to fit into the Delft furnace, keeping in mind all the constraints that brought with it, and the user sample constraints too: the samples were 12 mm in diameter and 300 μm wide, while the space in the furnace was only 3 mm wide. In addition to this, a thermocouple spot needed to be spot-welded to the sample to monitor the temperature. The maximum temperature to be reached was 800 °C.
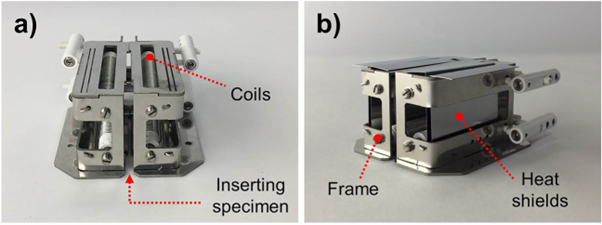
Harry worked in collaboration with the users and Simon in the R6 workshop to meet the design requirements. To reduce scatter, it was constructed from a neutron absorber, specifically boron nitride which is a machinable ceramic with tolerance in the right temperature range.
The final design (below) features a recess for the sample, channel for the thermocouple and allows the sample to slide into place with a dovetail joint for ease of access.
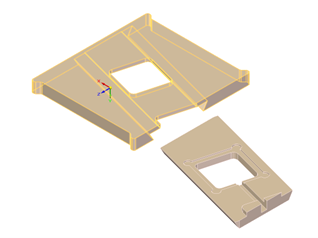
The furnace cores needed manufacturing and assembling, and spare insulator components were provided. Winding the molybdenum wire around the boron-threaded insulators proved difficult but not impossible.
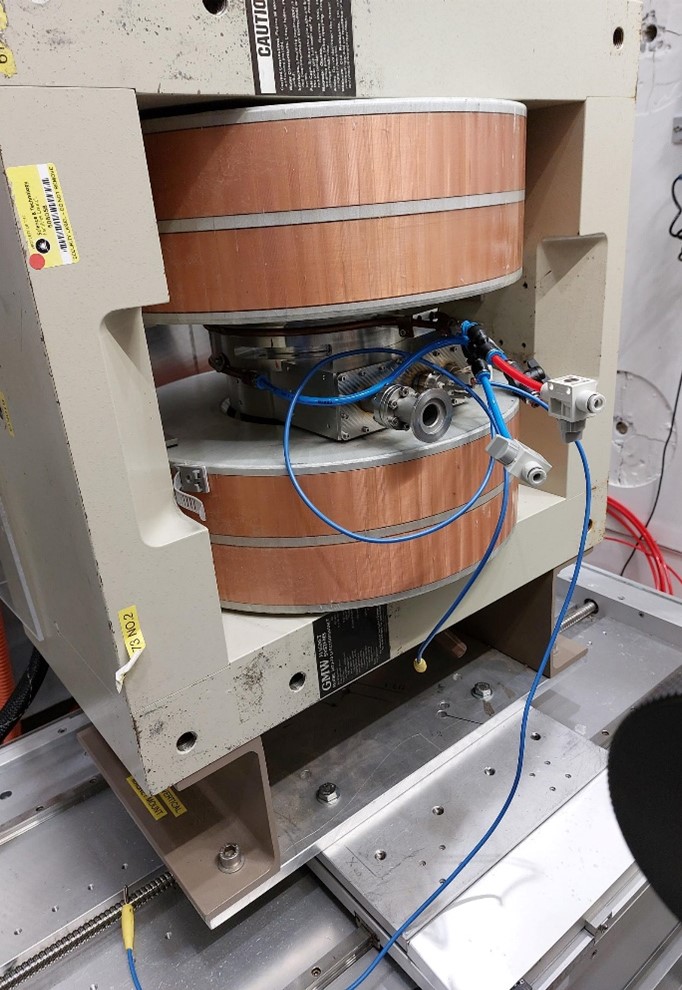
This equipment allowed the user measurements to be run successfully. The Soft Matter team would like to thank the Pressure and Service team for use of their spot welder.
For more information about these projects, or any other enquiries to the Soft Matter team, please
contact team leader Andy Church and check out the Soft Matter Team
website.